KTI Project ALSTOM – Solar-Driven Gas Turbine
Funding source: external page CTI-Innovation Promotion Agency
Partners: external page ALSTOM
Background:
The direct supply of concentrated solar energy to a gas turbine, e.g. for driving a combined Brayton-Rankine cycle, offers high solar-to-electricity conversion efficiency and, consequently, high potential for power cost reduction. To reach the required temperatures and pressures of the working fluid at the gas turbine inlet – typically in the range 1000-1600 K and 5-30 bar – solar receivers have been proposed for solar towers and dishes based on the direct (windowed) or indirect-irradiation concept. Direct-irradiation solar receivers offer evidently high heat transfer rates; however, they require a transparent window for the optical access of concentrated solar radiation, which is a troublesome and critical component. Indirect-irradiation receivers eliminate the need of a window by using opaque heat exchangers but at the expense of conduction-limited heat transfer rates through the solar absorber walls. Thus, the disadvantages are linked to the limitations imposed by the materials of construction of the solar absorber such as the maximum operating temperature, thermal conductivity, resistance to thermal shocks, and inertness to oxidation by air. A novel design concept of an indirect-irradiated solar receiver is proposed. It consists of an annular reticulate porous ceramic (RPC) foam concentric with an inner cylindrical cavity-receiver exposed to concentrated solar radiation. Absorbed heat is transferred by combined conduction, radiation, and convection to the pressurized air flowing across the RPC.

Objective:
Project aimed at the engineering development of a 30 kW solar receiver for heating compressed air to the entrance conditions of a gas turbine. The receiver development work involves:
- design
- fabrication
- testing
- modeling and validation
- optimization
- system integration
Project Description:
1st Phase: Receiver Design & Construction
The 1st phase of the project consists of the design and fabrication of a solar receiver prototype for an input solar power of 30 kW. The peripheral equipment such as the air circuit system will be integrated to the receiver. The measurement & data acquisition system will include temperature, pressure, gas flow, and radiative flux measurement devices, experimental control and safety devices. The measurement locations and safety criteria will be determined.
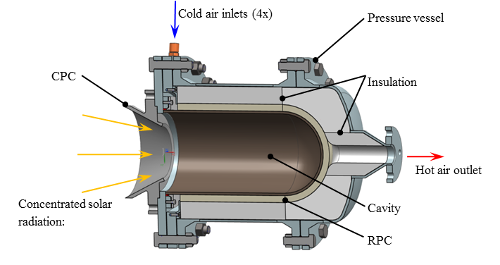
2nd Phase: Experimental Demonstration
The 2nd phase of the project consists of the receiver set-up and solar experimentation. The complete system, comprised of the solar receiver, the measurement and data acquisition system, and various peripheral components, will be assembled and installed at the experimental site. Experimentation will take place at a solar tower facility. The measurement and data acquisition system for monitoring the performance of the process will be made operational. The receiver system will be tested for various operating temperatures and mass flow rates. Energy balance will be performed for each experimental run. The receiver performance will be evaluated according to its (solar-to-heat) thermal efficiency.
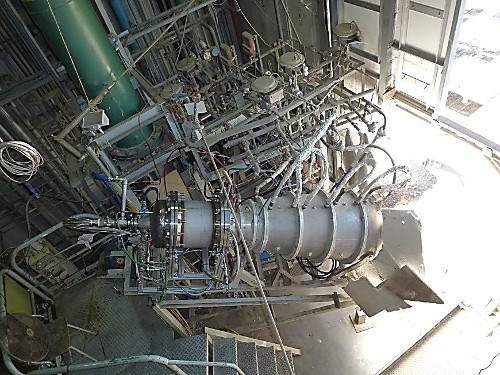
3rd Phase: Receiver Modeling, Validation, & Optimization
This phase will address the solar receiver modeling for predicting its performance and for optimizing its design. Predictions will be a function of receiver design variables such as the solar concentration ratio and receiver geometry as well as receiver's operating parameters such as temperature, pressure, mass flow rate, and solar power input. The performance output that will be evaluated includes the thermal efficiency, and the temperature and flow distributions within the receiver. Model validation will be accomplished by comparing theoretical and experimental results with the 30 kW prototype tested. The work encompasses the following tasks:
- Modeling – Apply existing heat transfer and fluid flow model for a given set of boundary and initial conditions. Establish the radiation exchange inside the receiver using Monte-Carlo ray tracing. Through iteration, link the solution to the radiation exchange to the convective-conductive heat transfer.
- Validation – Compare numerical results with those obtained experimentally with the 30 kW prototype receiver. The solar flux measurements at the focal plane will be used to validate the Monte-Carlo (MC) ray tracing simulation model.
- Optimization – Carry out a parametric study for optimizing design and operation of the solar receiver for maximum thermal efficiency. The parameters are: dimensions, solar power and power fluxes, temperature, pressure, and mass flow rates.
- Up-scaling – Use the system model for predicting temperature profiles and thermal efficiency of the pilot (1 MW) and commercial (10 MW) receiver system using an array of 30 kW modular receivers.
4th Phase: System Integration & Analysis
This phase will deal with the analysis of the integrated solar combined cycle, with or without thermal storage. Dynamic simulations that account for the intermittence of solar radiation will be performed to predict solar-to-electricity system efficiencies.
Project-related Publications